POLYSTAR to demonstrate ABA 3 layer co-extrusion Eco-Flex in Plastvision Arabia 2016
ABA Blown Film Technology: Thinner, stronger film at lower production cost
Following a successful exhibition in Arabplast 2015, POLYSTAR will again demonstrate its blown film extrusion and recycling lines in the exhibition in Sharjah in February 2016, Plastvision Arabia. Many film producers have adopted the ABA blown film technology as a replacement of monolayer machines nowadays, mainly because a high percentage (up to 50~70%) of CaCO3 compounds an be used in the B (middle) layer of the film. This significantly cuts down the usage of virgin raw material and thus reduces production cost.
In 2015, Polystar and its representative in Russia Evropolimer has already carried out more than 10 installations of 3 layer ABA blown film extrusion machines in different industrial areas of Russia. With the third consecutive year of increased number in sales, repeated orders and positive customer feedback, it is evident that ABA is extremely competitive for manufacturing T-shirt and garbage bags comparing to mono (one) layer production. In markets where the price of HDPE raw material has increased significantly, ABA provides a great advantage in terms of lowering production cost and increasing product quality and competiveness. Polystar looks to introduce this ABA technology in the UAE as well as GCC markets with. Customers will be able to see live demonstration of ABA during Plastivison Arabia.
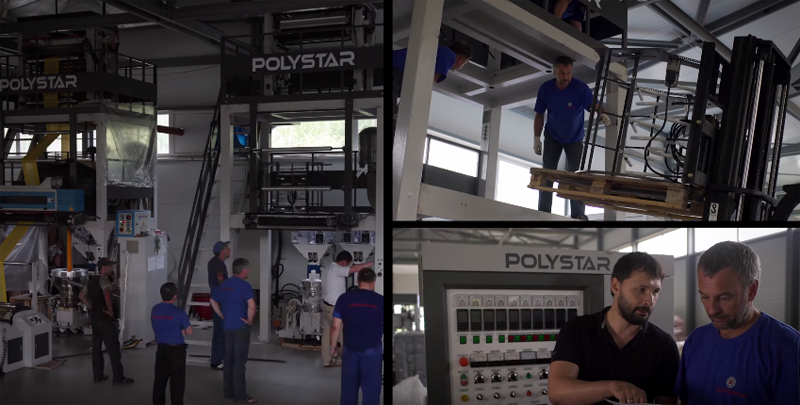
The main advantages of the ABA line are:
● Stronger, higher film resistance comparing to mono layer film products with the same thickness
● Cost saving: Virgin material is applied mainly on the outer (thin) layers which is relatively a very small percentage of the film composition
● Better material mixing with co-extrusion to produce better quality film
The main usage and applications of the ABA machines are:
● For the production of T-shirt bags, garbage bags and shrink film (for bottle wrapping)
● 60% CaC3 compounds or recycled material can be used in the middle layer
● Thin outer layers with virgin material to cover the film surface so that it still looks good and shinny despite the usage of secondary grade material in the middle layer

The ABA blown film extruders consists of two extruders to produce 3-layer film.
The most common ones today are the combination of a 45mm extruder together with a 55mm to produce 500~1000mm film width, and a 55/65mm extruder combination to produce up to 1400mm film in width, particularly for the production of T-shirt bag and garbage bags. The B (middle) layer, which makes up about 60~75% of the film composition, usually consists of 60~70% CaCO3 compounds. Recycled pellets (from in-house waste) can also be added to the blend. The re-designed screw helps to achieve maximum efficiency during the film production process. A better extrusion mixing is able to produce outstanding film quality, even when working with 60% CaCO3 and recycled material in the mixture.
A key focus: ABA 3 Layer
Following a successful exhibition in Arabplast 2015, POLYSTAR will again demonstrate its blown film extrusion and recycling lines in the exhibition in Sharjah in February 2016, Plastvision Arabia. Many film producers have adopted the ABA blown film technology as a replacement of monolayer machines nowadays, mainly because a high percentage (up to 50~70%) of CaCO3 compounds an be used in the B (middle) layer of the film. This significantly cuts down the usage of virgin raw material and thus reduces production cost.
In 2015, Polystar and its representative in Russia Evropolimer has already carried out more than 10 installations of 3 layer ABA blown film extrusion machines in different industrial areas of Russia. With the third consecutive year of increased number in sales, repeated orders and positive customer feedback, it is evident that ABA is extremely competitive for manufacturing T-shirt and garbage bags comparing to mono (one) layer production. In markets where the price of HDPE raw material has increased significantly, ABA provides a great advantage in terms of lowering production cost and increasing product quality and competiveness. Polystar looks to introduce this ABA technology in the UAE as well as GCC markets with. Customers will be able to see live demonstration of ABA during Plastivison Arabia.
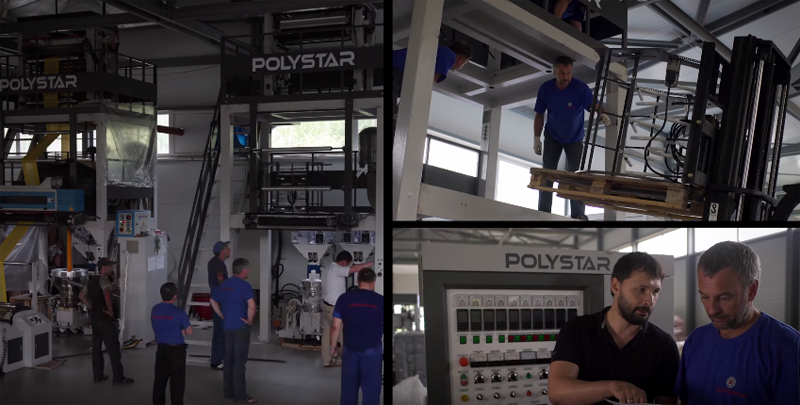
The main advantages of the ABA line are:
● Stronger, higher film resistance comparing to mono layer film products with the same thickness
● Cost saving: Virgin material is applied mainly on the outer (thin) layers which is relatively a very small percentage of the film composition
● Better material mixing with co-extrusion to produce better quality film
The main usage and applications of the ABA machines are:
● For the production of T-shirt bags, garbage bags and shrink film (for bottle wrapping)
● 60% CaC3 compounds or recycled material can be used in the middle layer
● Thin outer layers with virgin material to cover the film surface so that it still looks good and shinny despite the usage of secondary grade material in the middle layer

The ABA blown film extruders consists of two extruders to produce 3-layer film.
The most common ones today are the combination of a 45mm extruder together with a 55mm to produce 500~1000mm film width, and a 55/65mm extruder combination to produce up to 1400mm film in width, particularly for the production of T-shirt bag and garbage bags. The B (middle) layer, which makes up about 60~75% of the film composition, usually consists of 60~70% CaCO3 compounds. Recycled pellets (from in-house waste) can also be added to the blend. The re-designed screw helps to achieve maximum efficiency during the film production process. A better extrusion mixing is able to produce outstanding film quality, even when working with 60% CaCO3 and recycled material in the mixture.
A key focus: ABA 3 Layer
Polystar has put a major emphasis on the re-designing and manufacturing of ABA blown film extruders in recent years. Approximately 135 sets of Polystar ABA type blown film extruders have been installed worldwide, particularly in countries where monolayer film production has become competitive. Polystar provides high customization on the ABA machines depending on customer’s requirement, space and budget concerns.
E-mail: [email protected]
(send us an inquiry on ABA blown film machine)